Our Blogs
PVC vs. TPO Roofing for Florida Businesses: A Detailed Comparison 🏢
🏢 Flat or low-slope roofs dominate Florida’s commercial landscape, from retail centers to industrial warehouses. And in the world of single-ply membranes, two contenders often top the list: PVC (Polyvinyl Chloride) and TPO (Thermoplastic Polyolefin). Both promise excellent weather resistance, energy efficiency, and cost savings over traditional roofing. But which membrane stands up better to Florida’s scorching sun, heavy rains, and occasional hurricanes? In this comprehensive comparison, we’ll examine the properties, pros, and cons of PVC vs. TPO, focusing on critical factors like durability, installation ease, and maintenance requirements—so you can make an informed decision that protects your business and your bottom line.
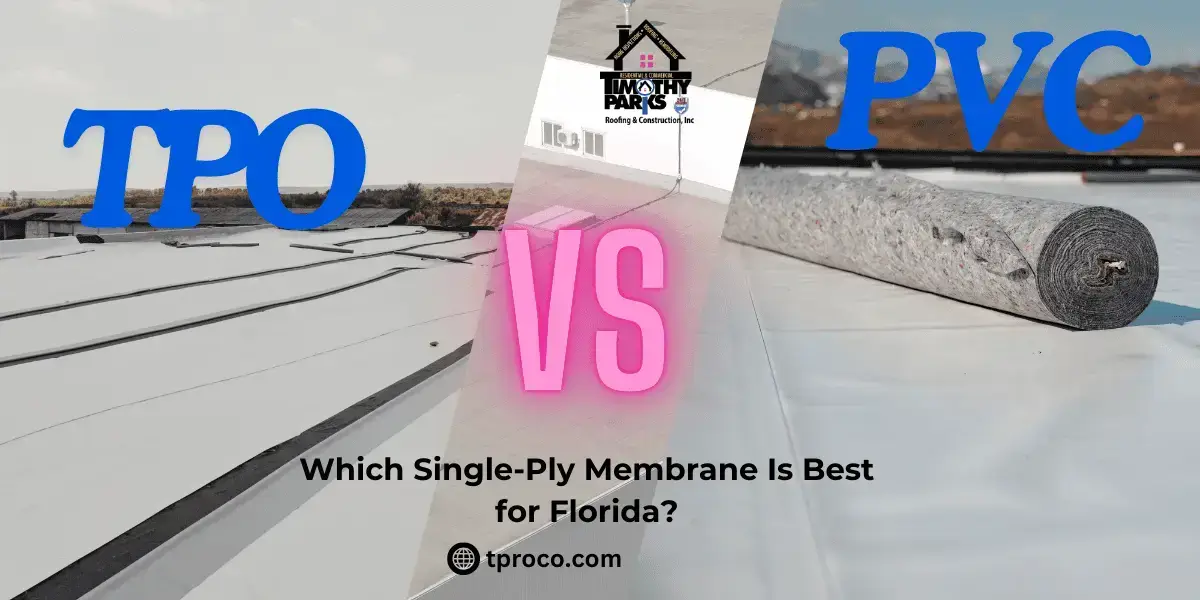
Overview of PVC Roofing
PVC membranes are crafted from polyvinyl chloride resin, combined with plasticizers for flexibility:
1. Key Characteristics
Chemical Resistance: Ideal for facilities handling fats, oils, or harsh chemicals. PVC doesn’t degrade easily when exposed to industrial byproducts.
Longevity: Thick, reinforced PVC can last 20–30 years with proper maintenance.
Heat-Welded Seams: Hot-air welding fuses sheets together, creating a watertight bond that resists leaks.
2. Advantages for Florida
UV Reflectivity: White or light-colored PVC reflects sunlight, helping lower cooling costs.
Resists Ponding Water: A well-installed PVC membrane can handle standing water without significant degradation, a plus for flat roofs during heavy rainstorms.
Fire Retardancy: PVC is known for self-extinguishing properties if ignited, offering extra safety.
3. Potential Drawbacks
Higher Cost: PVC membranes often command a premium price compared to TPO.
Plasticizer Migration: Over many years, plasticizers can evaporate, potentially leading to membrane brittleness if not well-formulated.
Chemical Emissions During Manufacturing: PVC production raises environmental concerns, though some brands focus on greener processes.
Understanding TPO Roofing
TPO roofing, made from a blend of polypropylene and ethylene-propylene rubber, has gained popularity for its cost-effectiveness:
1. Key Characteristics
Single-Ply Thermoplastic: Like PVC, TPO membranes can be heat-welded for strong seams.
Flexibility & Color Options: Typically sold in white, gray, or tan, with white being the most reflective.
Reinforced Scrim: Many TPO products include a fiberglass or polyester mesh for added tear resistance.
2. Advantages for Florida
Cost-Effective: TPO usually comes in cheaper than PVC, making it attractive for budget-conscious projects.
Energy-Efficient: Highly reflective surfaces help reduce heat absorption, lowering HVAC usage.
Weldable Seams: Seam integrity can approach that of PVC if proper welding techniques are used.
3. Potential Drawbacks
Variability in Formulations: Some early TPO versions suffered from issues like cracking or seam failures under UV exposure.
Less Chemical Resistance: Not the best choice if your facility deals with oils, fats, or harsh solvents that could degrade TPO.
Lifespan Uncertainty: While improved over the years, TPO membranes may not always match the 20–30-year track record of high-grade PVC.
PVC vs. TPO: Head-to-Head Comparison
1. Durability & Weather Resistance
PVC: Known for excellent wind uplift performance, chemical resistance, and proven longevity. Less likely to degrade under ponding water.
TPO: Offers good wind resistance when installed correctly but can be more vulnerable to environmental factors if the formulation is subpar. Modern TPO has improved to withstand harsh UV.
2. Installation & Weldability
PVC: Welding temperature is slightly lower than TPO, which can provide a margin of error for contractors.
TPO: Requires tighter control of welding temperatures; inexperienced crews might struggle to form perfect seams. However, skilled teams can achieve strong, reliable welds.
3. Energy Efficiency
Both: Offer reflective surfaces that meet or exceed ENERGY STAR® and LEED requirements for cool roofing. White membranes reduce heat gain in Florida’s sun.
Slight Edge: PVC generally has a slightly higher reflectivity rating out of the factory, though differences are minor in real-world conditions.
4. Cost & ROI
PVC: Higher upfront material cost, but can yield a longer lifespan and better chemical resistance—potentially a wise choice for certain industries.
TPO: Typically cheaper, making it attractive for large commercial roofs on a tight budget, provided the brand and formulation are reputable.
5. Environmental Impact
PVC: Critics point to chlorine-based manufacturing. However, recycling programs do exist, and some brands have reduced harmful additives.
TPO: Contains no chlorine, often touted as a “greener” option, but disposal and raw material sourcing still carry environmental footprints.
Installation Considerations for Florida
Regardless of membrane type, certain factors are crucial in the Sunshine State:
1. Deck Preparation
Smooth Surface: Insulation boards or cover boards must be level; debris or protrusions can puncture the membrane.
Proper Fastening or Adhesives: Meeting wind-uplift codes (110–150 mph in many areas) is mandatory.
2. Edge Detailing & Flashing
Metal Edge Systems: Must be secured and flashed to handle high wind loads.
Parapet Walls & Vents: The interface between vertical surfaces and the membrane is often a leak hotspot—professional attention is key.
3. Seam Quality
Heat Welding: Consistent, thorough welds form the backbone of single-ply integrity.
Overlap & Patching: Some TPO or PVC membranes require additional tapes or adhesives at joints; follow manufacturer guidelines.
4. Drainage & Slope
1/4" per Foot: Florida’s heavy rains demand adequate slope to prevent ponding water, which can stress membranes over time.
Scuppers or Internal Drains: Keep them clear to avoid backups that compromise roof performance.
Maintenance & Lifespan
1. Regular Inspections
Twice a Year & After Storms: Spot-check for mechanical damage, debris, or seam issues.
Professional Roof Audits: Some warranties require annual or biannual inspections by certified contractors.
2. Cleaning & Debris Removal
Prevent Ponding: Clear drain inlets and remove leaves or branches that trap water on the membrane.
Algae or Dirt: Periodic rinsing can maintain reflectivity, though strong chemicals might degrade the membrane if misused.
3. Seam and Flashing Repairs
Small Patches: Minor damage can be fixed with heat-welded patches or manufacturer-approved adhesives.
Routine Sealant Replacement: Certain penetrations or edge laps might need fresh sealant over time.
4. Warranty Coverage
Manufacturer Programs: High-quality membranes often come with 15–25-year warranties, contingent on approved installation and maintenance.
Contractor Workmanship Guarantees: Confirm the installation team offers a labor warranty covering seam failures or other defects.
Conclusion
🏢 Choosing between PVC and TPO for your Florida commercial roof ultimately hinges on your priorities—cost, chemical resistance, lifespan, and desired warranty coverage. PVC’s proven track record for durability and chemical tolerance can justify its higher upfront price, especially for facilities exposed to grease or harsh substances. TPO, meanwhile, delivers robust protection at a lower cost, appealing to many business owners on a budget. Whichever route you take, proper installation, adherence to local wind-uplift codes, and consistent maintenance are the true keys to maximizing performance. Take time to evaluate your building’s specific needs and consult reputable contractors; with the right choice, your new single-ply membrane will keep your Florida enterprise safe, dry, and energy-efficient for years to come.
Frequently Asked Questions (FAQ)
Weighing PVC vs. TPO?
Share your questions or experiences with single-ply membranes in Florida! Post your thoughts below or tag us on social media using:
#tproco #tppro #tprci #urro #rrfl
#PVCRoof #TPORoof #CommercialRoofing#FloridaBusinesses #TampaConstruction #OrlandoIndustry
Schedule a Free InspectionAbout the Author

Timothy Parks
CEO
📢 Stay Informed: Communication & Consent Updates
At Timothy Parks Roofing & Construction Inc., we prioritize transparency in our communications. By submitting a request, you agree to receive calls, texts, and emails regarding our services. Standard messaging rates may apply. You can opt-out at any time by replying STOP or contacting us directly.
âś… Florida License: #CBCO59592, #CCC1327217, #HI4878
📌 Privacy & Terms: Read our Privacy Policy and Terms of Service.