Our Blogs
Florida Flat Roof Solutions: TPO, PVC & Modified Bitumen Explained 🏭
🏭 Flat or low-slope roofs are a mainstay for Florida’s commercial buildings, multifamily complexes, and even some modern-styled homes. However, the same design that simplifies equipment mounting (like HVAC units) can also collect ponding water if not properly pitched—leading to leaks and rapid material degradation under Florida’s intense sun. Enter TPO, PVC, and modified bitumen membranes: three popular roofing systems offering robust waterproofing, reflectivity, and cost efficiency. In this guide, we’ll detail how each membrane fares against the Sunshine State’s punishing trifecta of heat, humidity, and storms, plus walk you through installation best practices to maximize longevity. Whether you’re overseeing a commercial facility or upgrading a flat section on your home, you’ll discover the ideal approach for a watertight, energy-efficient roof that shrugs off Florida’s extremes.
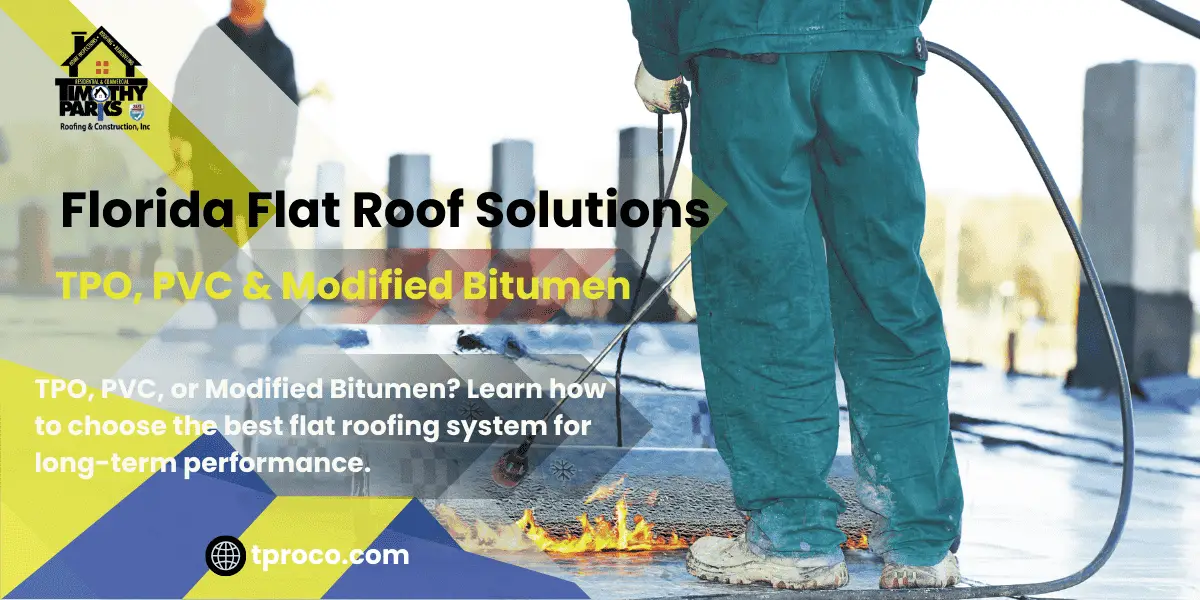
Unique Challenges of Florida Flat Roofs
Florida’s climate intensifies common flat roof vulnerabilities. Minimal slope means water can puddle in dips or uneven sections, and heavy rains or hurricane winds can push water into any small gap or seam. Over time, ponding water fosters algae or premature membrane wear if the roof material isn’t specified to handle standing moisture. Coupled with high UV exposure, surfaces crack or weaken if not UV-stabilized. Additionally, the warm, humid environment can trap moisture underneath membranes if vapor barriers or insulation layers aren’t carefully configured.
For commercial properties, rooftop HVAC equipment or foot traffic can also stress the membrane. Each footstep or shifted vent curb can scuff the surface, inviting leaks. Florida building codes demand high wind-uplift ratings—particularly in coastal zones—so how your membrane is fastened or adhered directly affects resilience. Ultimately, a successful flat roof in Florida must handle heat, humidity, ponding water, and storm gusts simultaneously. The right material, installation, and maintenance routine ensures you avoid frequent leaks or the dreaded full replacement years earlier than necessary.
TPO vs. PVC vs. Modified Bitumen: Pros & Cons
1. TPO (Thermoplastic Polyolefin)
- Reflectivity: Typically white or light-colored, TPO is great at bouncing away solar heat, lowering cooling costs.
- Seam Welding: Heat-welded seams create a continuous watertight barrier, crucial for withstanding Florida downpours.
- Cost & Durability: Generally more affordable than PVC, though older or lower-grade TPO formulas can degrade if not properly UV-stabilized. High-quality TPO can last 15–20 years or more with good maintenance.
2. PVC (Polyvinyl Chloride)
- Superior Chemical Resistance: PVC resists grease or chemical spills, ideal for restaurants or industrial sites.
- Longevity: Often outlasts TPO by a few years due to robust formulation, though it also costs more.
- Wind Uplift Performance: Like TPO, seams are hot-air welded, forming strong joins that handle Florida’s high winds. Properly installed PVC membranes can surpass 20+ years.
3. Modified Bitumen
- Asphalt-Based Sheets: These single or multi-ply rolls combine asphalt with modifiers (APP or SBS) for flexibility. Usually torch-applied or cold-adhered.
- Ponding Limitations: Standing water accelerates wear if the surface isn’t well-protected. Light-colored or mineral surfaces can reflect some heat, but typically less than TPO/PVC.
- Cost & Familiarity: Roofers have used modified bitumen for decades, so it’s widely available, though not as reflective or seamlessly welded as modern thermoplastics.
- Durability: With a robust base sheet and consistent coverage, it can endure Florida’s storms but may need extra slope or drainage improvements to avoid ponding.
Choosing among these depends on budget, reflectivity goals, chemical exposure, and your roof’s slope or complexity. For large commercial buildings, TPO and PVC stand out for easy installation and strong reflectivity. Modified bitumen remains a valid option for smaller or budget-driven projects, especially if you’re comfortable addressing ponding issues and fewer color options.
Installation Best Practices for Florida Flat Roofs
No matter which membrane you choose, proper installation is vital under Florida’s code demands and weather extremes:
- Surface Prep & Slope: Ensure the decking or substrate is clean, dry, and free of old adhesives. Patch dips or uneven areas so water flows to drains or scuppers. Minimum slope of 1/4" per foot helps water shed instead of puddling.
- Underlayment or Insulation: Rigid insulation boards can enhance energy efficiency and create a smoother surface. Foam adhesives or fasteners must meet wind-uplift standards. Some roofs use cover boards to improve puncture resistance.
- Seam Welding or Overlaps: TPO/PVC require hot-air welding for reliable seams. Overlapping edges by at least 2–3 inches is common. For modified bitumen, torch or cold-adhesive overlaps must be consistent, with no voids where water can seep in.
- Flashings & Penetrations: HVAC units, drains, and parapet walls need specialized flashing. Heat-welded boots around pipes or carefully layered bitumen in corners prevents leaks at these vulnerable points. Skylights or chimneys also demand thorough sealing.
- Perimeter & Corner Reinforcement: Florida’s building code emphasizes the roof perimeter, where wind uplift is highest. Extra fasteners, plates, or membrane strips are often required. Double-check manufacturer instructions for corner detailing—these spots frequently fail if shortcuts are taken.
A thorough approach means fewer callbacks and longer intervals before re-roofing. Hiring a roofer experienced with local HVHZ (high-velocity hurricane zone) compliance ensures your new flat roof stands strong against tropical onslaughts.
Maintenance & Leak Prevention
Flat roofs can perform admirably if inspected and maintained regularly—especially in Florida’s environment:
- Clear Debris & Drains: Leaves, branches, or palm fronds block drains, creating ponding water. Clean them every few months, or more often after storms.
- Check Seams & Flashing: TPO/PVC welds sometimes show hairline separations over time; modified bitumen overlaps can lose adhesion. Promptly patch any gaps with manufacturer-approved tapes or new welded patches.
- Monitor Ponding Spots: If water remains more than 48 hours after rainfall, investigate slope issues. Add leveling compounds or internal drains if needed. Chronic ponding invites algae, membrane decay, and extra weight on the deck.
- UV or Sealant Recoats (If Applicable): Some modified bitumen surfaces benefit from periodic reflective coatings. Keep these coatings in good shape to minimize heat absorption and prevent asphalt drying out.
An annual or semi-annual inspection helps you catch small cracks or lifted edges before they blossom into major leaks. Overlooking these tasks might mean water saturates insulation layers or spreads moldy conditions inside the building. In Florida’s wet climate, a little proactive care goes a long way in safeguarding a flat roof’s function and longevity.
Conclusion
🏭 Flat roofs in Florida face downpours, blazing UV, and hurricane-force winds—but modern membranes like TPO, PVC, or modified bitumen can thrive if installed and maintained with care. By choosing a membrane suited to your budget, slope, and reflectivity needs, you’ll keep water at bay and manage attic or interior temperatures more effectively. Pair that with strategic drainage solutions, robust welding or overlapping, and routine checks to clear debris, and you’ll significantly cut the risk of leaks or premature wear. Ultimately, a well-constructed flat roof stands strong against Florida’s harsh elements, safeguarding both your property and your peace of mind.
Frequently Asked Questions (FAQ)
🏭 Choosing the Right Flat Roof for Florida?
TPO, PVC, or Modified Bitumen—which is best? Learn how these durable, waterproof roofing systems handle Florida’s heat, humidity, and storms to keep your building protected:
#tproco #tppro #tprci #urro #rrfl
#FlatRoof #TPO #PVCroof #FloridaConstruction #TampaCommercial #SunshineState
Schedule a Free InspectionAbout the Author

Timothy Parks
CEO
📢 Stay Informed: Communication & Consent Updates
At Timothy Parks Roofing & Construction Inc., we prioritize transparency in our communications. By submitting a request, you agree to receive calls, texts, and emails regarding our services. Standard messaging rates may apply. You can opt-out at any time by replying STOP or contacting us directly.
✅ Florida License: #CBCO59592, #CCC1327217, #HI4878
📌 Privacy & Terms: Read our Privacy Policy and Terms of Service.